On many bridge construction projects, cranes are sometimes the best and only option for moving heavy items around a site. But there are many situations when alternative equipment is needed.
The limitations of cranes for bridge construction include:
- Poor Accessibility: A generous amount of space is needed to position and operate a crane, which can be difficult in areas with limited access or tight spaces.
- Height restrictions: Cranes lift the load from above, so the height of cranes limits their usefulness on projects involving overhead obstacles, such as cables or underneath a roof structure.
- Weight restrictions: Cranes have capacity restrictions that can limit their ability to lift very heavy bridge components.
- Weather conditions: Strong winds, heavy rain, or extreme temperatures affect the stability and safety of crane operations, making it difficult to work in certain conditions.
- Cost: Cranes can be expensive to rent or purchase, and their high operating costs can add up quickly.
What are the alternatives to cranes?
Precise lifting and positioning are crucial during bridge and highway construction. While cranes are the mainstay of many projects, in some cases the use of a crane is impractical or simply too expensive, especially due to the extensive transportation logistics required to get all crane parts to the construction site.
Various alternative lifting systems exist and are proving increasingly efficient, these include:
Hydraulic Strand Jacks: Compact, easy to transport, and powerful enough to lift loads of over 3,000 tonnes without difficulty.
Hydraulic Gantries: Using four or more telescopic legs and beams that allow heavy loads to be lifted vertically, and along a track when required.
Jack-Up Systems: Lifting loads in successive stages using spacers, called “barrels”, stacked together to form lifting towers t0 mechanically support the load.
Described below are examples of where these alternative lifting technologies were used.
Jack Up System Ensures Accuracy during 2800 Tonne Lift
Italian Company Fagioli, which specializes in heavy load transport, design, and handling of special and mammoth structures, used an Enerpac JS-500 Jack-Up system to transport, lift and install the 2,800-tonne bridge section for the new San Benedetto PO bridge in Mantua.
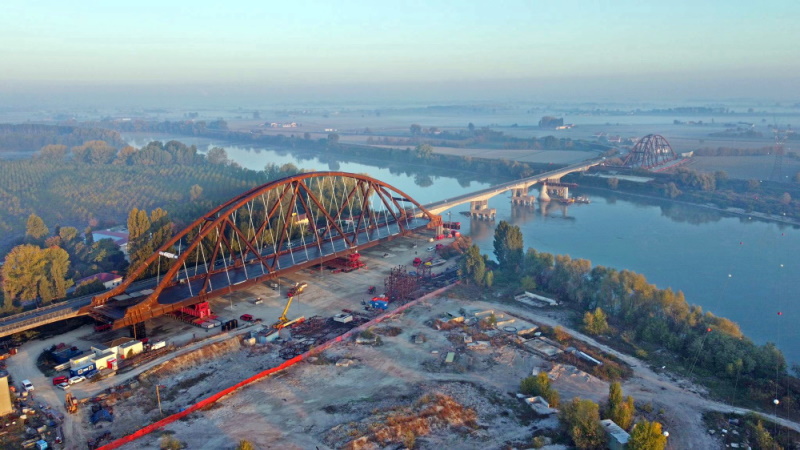
Eight legs of the jack-up system lifted the 590 feet (180-metre) long bridge in synchronization and positioned it safely on site. The span was lifted by a jack-up system which allowed SPMTs to be inserted: these trailers then transferred the span section to a dedicated barge equipped with towers and other SPMTs for alignment with the piers positioned in the river.
Bridge Construction Using A Hydraulic Gantry Overcomes Access Issues
Lacking space for a large and capable mobile crane, heavy lifting equipment rental company, LGH, used its hydraulic gantry to remove the Steenhuisenbrug bridge in Burdaard, Friesland, The Netherlands. Mounted on a pontoon, the Enerpac SL100 gantry provided a stable lift for the 48-tonne bridge and its transport.
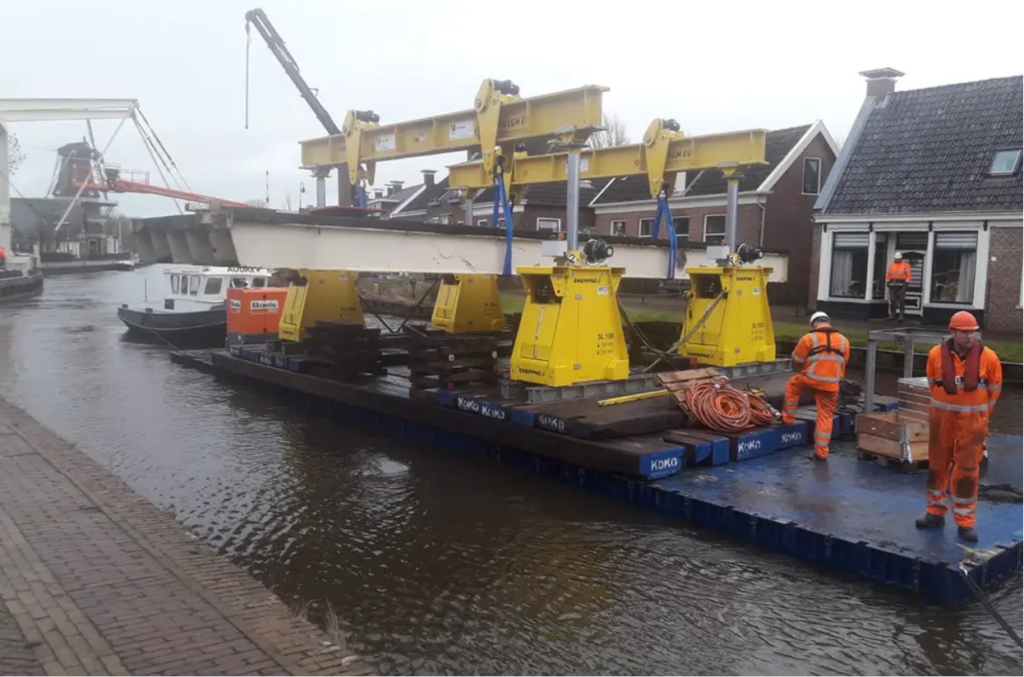
LGH’s client was unable to use the mobile crane normally used for this type of lifting due to logistics and construction site encumbrances: the Enerpac SL100 gantry proved perfect for the project.
Positioned on a pontoon on either side of the bridge, slings suspended from the gantry header beams were attached to the bridge. Using the gantry’s wireless controller, the bridge deck was lifted clear of the bridge and the pontoon was rotated, allowing the bridge deck to be moved 328 ft (100 m) along the waterway. The bridge was then lifted with a crane onto nearby land to be refurbished over the next 6 weeks.
Saving Time Building and Installing an Inclined Bridge Deck
An eight-point Enerpac jack-up system allowed the Osprey Group, a leader in logistics and heavy transport, to complete the installation of a bridge deck in one move. Even with a 5 ft (1.5 m) height difference at both ends of the bridge, the Enerpac JS-250 Jack-up system successfully lifted the 1,400-tonne load.
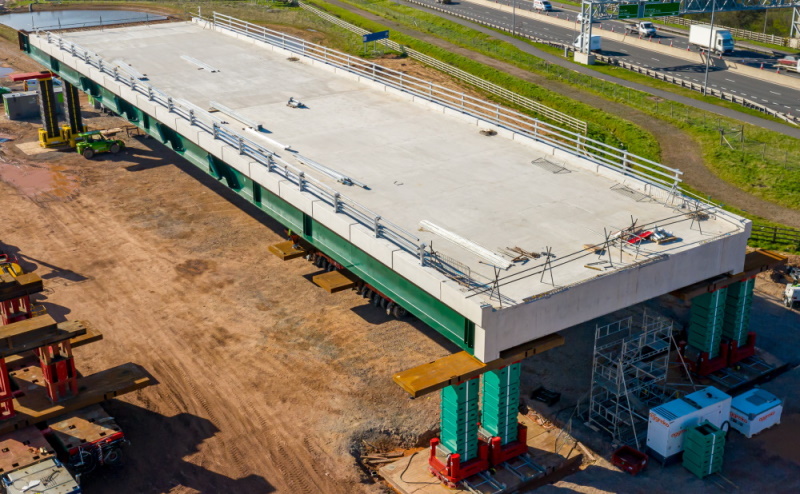
The 74 m long and 16 m wide deck replaced an existing bridge over a dual carriageway. Using the JS-250 jack-up system allowed the deck to be built alongside the highway and transported on SPMTs to the installation site. The jack-up units were easily delivered to the deck construction site by flatbed trucks, without requiring multi-specialized transport.
The installation of the bridge was completed within a weekend. With four JS-250 Jack-Ups at each end, the bridge deck was lifted and then transported 500 m to the bridge abutments on the dual carriageway by SPMT. It was essential to precisely position the bridge deck at 22 ft (6.8 m) at the point of maximum inclination with the Enerpac jacks. Once in position, the SPMTs were used for the final height positioning.
“The Enerpac JS-250 Jack-Up units are an indispensable piece of equipment for us. They are easy to deploy and operate,” said Ryan Ebanks, Project Engineer, Osprey Group. “Given the size of the deck in this case and the need to tilt it by 1.5m, the Enerpac jack-up was a perfect choice. Without it, we would have had to use more cranes”.
The JS-250 Jack-Up system uses computerized controls for seamless synchronous control, raising and lowering all towers simultaneously. Capacities per tower of the JS Series Jack-Ups range from 125 metric tonnes to 750 metric tonnes. Lifting heights range from 16 to 20 meters respectively (19.2-65.6 ft).
Gantry Provides Stability During Strong Winds
Timing is crucial for railway construction projects to avoid unforeseen disruptions to rail and passenger services. However, the best project planning can be compromised by adverse weather conditions. Strong winds, typically those exceeding 19 km/h can prevent the lifting of a bridge by crane, causing project delays. To avoid delays, Osprey Heavy Lift Ltd used an Enerpac SBL900 gantry to prepare a replacement bridge section on the Chester line in the UK.
“The Enerpac gantry was the ideal lifting system for this bridge replacement project. Working at ground level and the ease of lifting the deck on an SPMT made a smooth installation of the new bridge deck possible,” said Nigel Fletcher, managing director of Osprey Heavy Lift Ltd.
Hydraulic gantries are commonly used for bridge repair and replacement. The tendency today is increasingly to build the new bridge close to where it is to be installed. Once completed, the bridge is lowered onto the SPMT for the short journey to the new location.
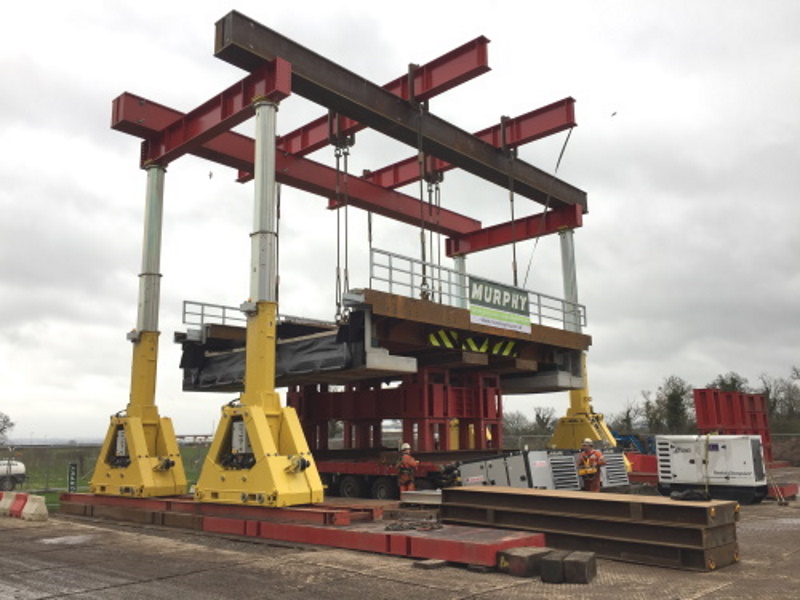
Hydraulic Gantry Keeps 320-Tonne Arch Rail Bridge Level During Rapid Construction
Royal Wagenborg used an Enerpac SBL500 Hydraulic Gantry to assemble a 320-tonne arch rail bridge across the A14 motorway in Germany. The 42 m long and 7 m wide (138ft x 23 ft) replacement steel arch bridge was built close to the motorway.
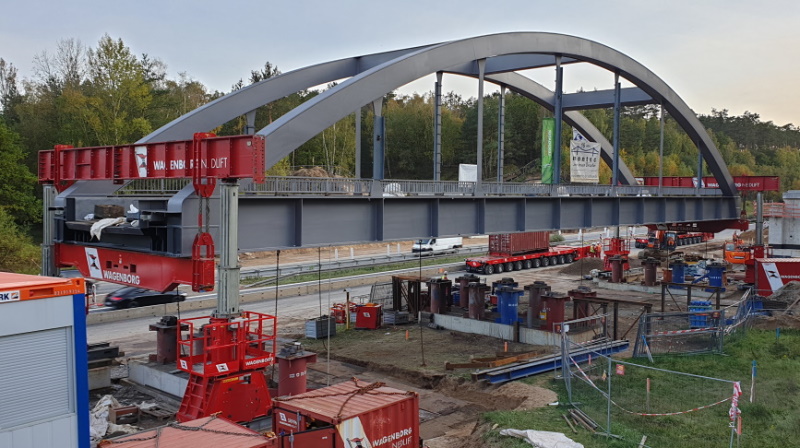
Using the SBL500 gantry allowed Royal Wagenborg to overcome the challenge of building the bridge on an inclined slope. The two ends of the bridge were held by the gantry at 6.9 m and 6.5 m respectively (22.6ft and 21.3 ft) – ensuring it remained level during construction.
Once completed, the gantry allowed the bridge to be quickly lowered to 4.5 m (14.7 ft) and placed on SPMT to be transported for final installation.
“The biggest challenge we faced was the narrow location near the A14 and transporting the equipment to the construction site. By using the SBL500 gantry, we were able to assemble the bridge much faster than with the jack-and-pack method. In addition, the gantry provided us with the necessary degree of control to keep the bridge level during construction” – says Bart Schutte, Project Manager at Wagenborg Nedlift.
Small Footprint Strand Jacks lift 613-tonne Pier Tables 205 Feet (62.5 m)
Enerpac strand jack technology was used to lift two 613-tonne pier tables to a height of 205 ft (62.5m) for the Gerald Desmond Bridge replacement project in Long Beach, California. The bridge has a cable-stayed structure based on two 515 ft (157m) steel and concrete towers. It is the second-tallest cable-stayed bridge in the United States and has the greatest vertical height of all cable-stayed bridges in the United States.
Enerpac HSL 5000 strand jacks lifted the pier tables of each of the two towers. These will form the east and west ends of the 2001 ft (610m) main span spanning the waterway. “It would have been impractical to use a crane, given the size and weight of the pillar planks. The strand jack is the best choice in terms of lifting capacity and cost,” said the heavy lifting company spokesperson.
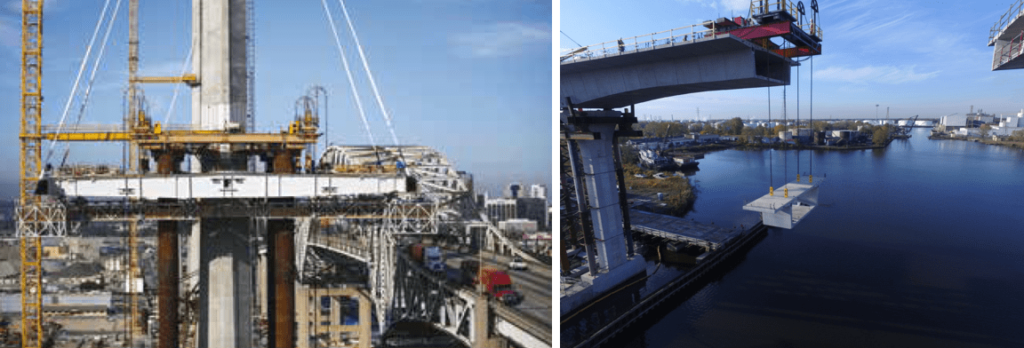
To prepare for the positioning of the strand jacks on the pier tables, a four-column ceiling was installed on each of the two towers. Enerpac HSL 5000 strand jacks, each with 48 steel strands, were positioned at each corner of the falsework to lift the steel-framed pier board. The synchronization of the strand jacks allowed all lifting positions to be raised simultaneously, ensuring the balance of the pier boards. The positioning of the piers required patience and precision; each stroke of the strand jack was 46 cm and the entire lifting of each pier table took ten hours.
The synchronized lifting was done via Enerpac’s SCC control system, which allowed the entire lifting to be managed by a single operator. The lifting was simple. However, maneuvering the pier board into its final resting position on the falsework was a delicate operation; the final alignment was coordinated with the strand jack and visual feedback from the engineers on the piers.
How a Hydraulic Gantry Works
An Enerpac hydraulic gantry consists of four or more telescopic Legs and a beam that allows heavy loads to be lifted vertically. If it is necessary to move the load horizontally, the entire gantry system and its load can be moved along a skidding track. Hydraulic gantries are an economical solution for many lifting and rigging applications.
Enerpac offers two types of hydraulic gantry systems for rail construction: the Super Lift (SL) Series for lifts up to 400 tonnes, and the Super Boom Lift (SBL) Series for up to 1100 tonnes.
How a Strand Jack Works
Hydraulic Strand Jack (HSL) Systems pack enormous lifting capacity into a small footprint and are easy to transport. In a strand jack, a bundle of steel cables (strands) are guided through a specially perforated hydraulic cylinder. Above and below the cylinder are hydraulic anchoring systems with wedges that safely grip the strand bundle. By actuating the cylinder while the wedges are engaged in the anchors, a raising or lowering movement is achieved. Learn more about how they work here.
Enerpac has perfected the strand jack technique by making it easier to use with automated locking and unlocking operations, as well as allowing synchronized, precision lifting and lowering by a single operator. In addition, the system software can control up to 60 cylinder/pump combinations, which means the potential for synchronous lifting on a large scale is significant.
How Jack Up Systems Work
Enerpac JS Series Jack-Up Systems have transformed the way many heavy-lifting projects are carried out. The jack-up system is a synchronized lifting and lowering system with a self-contained hydraulic system in each unit. This keeps working areas free of cables and various power packs. Loads are lifted in successive stages while steel spacers, called “barrels”, are stacked together to form lifting towers that mechanically support the load.
Summary
Alternative heavy lift systems offer the bridge contractor many more options than traditional cranes. Smaller, lighter and easier to transport, these are a powerful addition to the range of lifting solutions now available for road and rail bridge projects.
You can learn about more bridge construction projects by downloading the case study pack shown below.